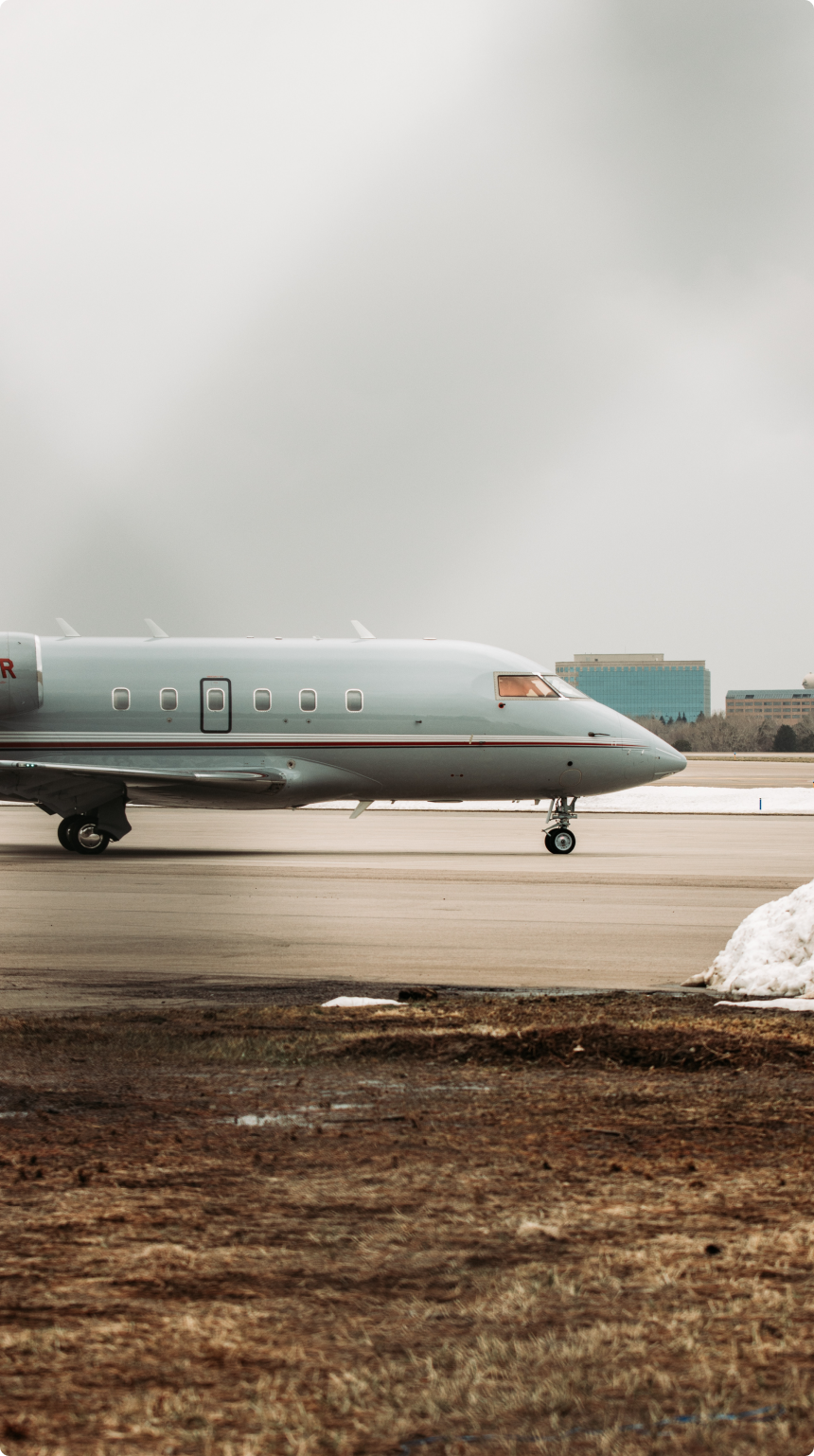
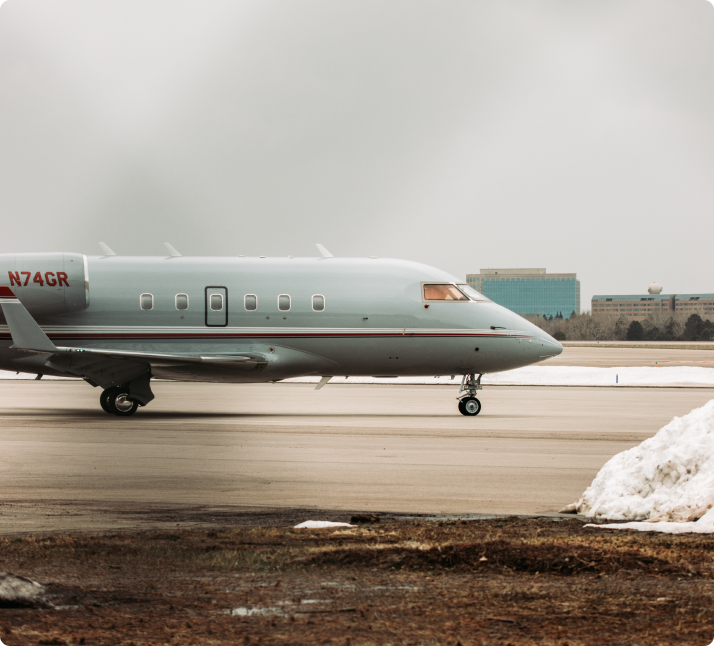
Qualification Testing
Ensure efficiency and safety for systems and components.
Improve efficiency and reduce cost with the convenience of our in-house qualification testing.
Our environmental testing labs can effectively simulate any environment on earth, ensuring that aircraft systems and components meet the required standards for safety and performance.
The benefits to your development process through our agile, in-house testing process include:
We value a very close relationship with our customers to ensure your project’s success.This relationship is supported by:
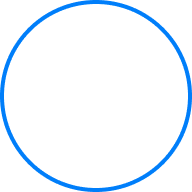
The ability to identify an area of risk during the design phase
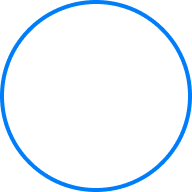
The capability to test this area early in the design cycle through an iterative process that includes mocking up prototypes and simulating a variety of conditions to gauge performance
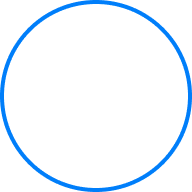
The ability to identify an area of risk during the design phase
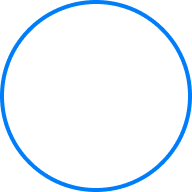
The capability to test this area early in the design cycle through an iterative process that includes mocking up prototypes and simulating a variety of conditions to gauge performance
This process helps to correct potentially costly design flaws quickly and with time to recover so that your product avoids scheduling delays and safety or performance issues down the road.
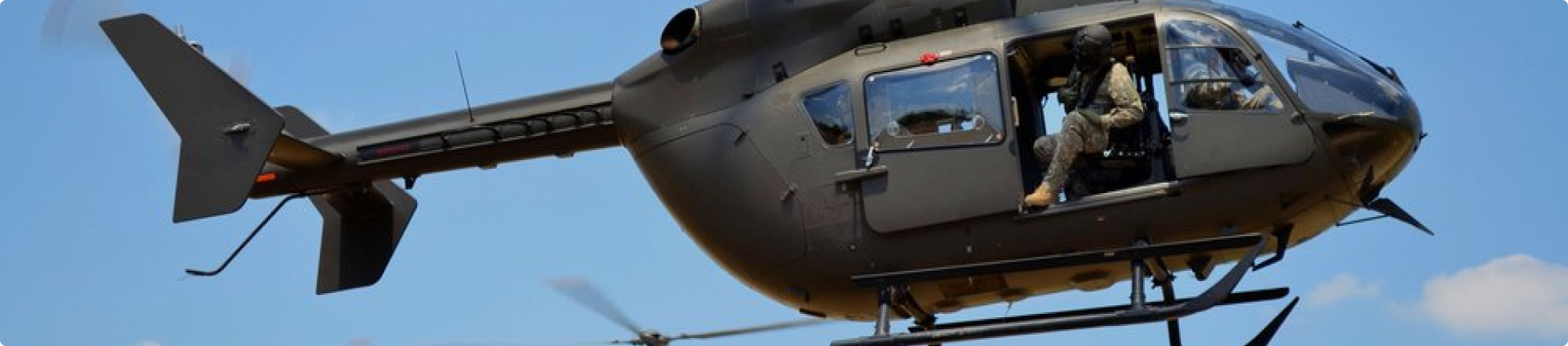
Testing solutions for systems and components
By operating our systems in our test lab, our engineers are able to ensure that your system designs achieve maximum efficiency and performance. This includes testing for:
- Optimization of superheating and sub-cooling settings
- Monitoring of the system’s response to atmospheric and air density changes
- Measurement of ducting and distribution changes
- Accountability of the effect of refrigerant plumbing routing and sizing
- Evaluation of changes to component selection and orientation
- Blower and fan performance testing
- Compressor volumetric efficiency testing
- Air-side and liquid-side psychrometric testing for Vapor Cycle Air-Conditioning (VCS) systems
- VCS system efficiency, performance and capacity optimization, and validation testing
- Psychrometric calorimeter testing with enthalpy potential monitoring
- Blower and fan performance and optimization testing
- Steady state performance testing
- Pull down performance testing
- Ducting and distribution performance optimization testing
- Compressor volumetric efficiency performance and optimization testing
- Heat exchanger and ducting pressure drop validation testing
- 10 CFR Part 430 testing
- Title 24 of California Energy Efficiency Testing
- ARI 210/240 air conditioning and air source heat pump testing
- ARI 340/360 performance testing and rating
- ARI 810/820 testing
Contact us about our testing facilities
RTCA DO-160 Testing
We have also invested in the capability to perform most RTCA DO-160 Environmental and Electrical requirements testing in-house. This capability enables us to reduce design risk and shorten development time.
DO 160 Section | Description | In-house test Capability |
---|---|---|
04 | Temperature and Altitude | Categories A1 through F3 |
05 | Temperature Variation | Categories A through C, S1 & S2 |
06 | Humidity | Categories A through C |
07 | Op. Shock | Categories A, B & D |
08 | Vibration | Categories S, H, Z, R, U & U2 |
09 | Explosion Proofness | Category H |
10 | Waterproofness | Categories Y, W, R & S |
15 | Magnetic Effect | All Categories |
16 | Power Input | Category Z |
17 | Voltage Spike | All Categories |
18 | Audio Frequency Susceptibility | Categories B, R & Z |
19 | Induced Signal Susceptibility | All Categories |
20 | Radio Frequency Susceptibility | Categories R & T |
21 | Emission of Radio Frequency | All Categories |
24 | Icing | Categories A & C |
25 | Electrostatic Discharge | All Categories |